โกศล ดีศีลธรรม
ผู้จัดการทั่วไป(General Manager)
บริษัท อีควิตี้ เซอร์วิสเซส แอนด์ โซลูชั่นส์ จำกัด(Equity Services and Solutions)
หลายคนในแวดวงอุตสาหกรรมมักคิดว่าปัญหาการหยุดเดินเครื่องจักรเล็กน้อย(Minor stoppage) เป็นพียงปัญหาเล็ก ๆ ที่มักถูกมองข้าม แต่สภาพสายการผลิตที่ประกอบด้วยเครื่องจักรจำนวนมากมายหลากหลายประเภท หากเกิดปัญหาดังกล่าวก็จะส่งผลกระทบต่อผลิตภาพรวมของระบบการผลิต ดังกรณีสายการผลิตอัตโนมัติประกอบเครื่องจักร 100 เครื่อง แต่ละเครื่องสามารถสร้างผลิตผล 10000 หน่วยต่อวัน โดยค่าเฉลี่ยอัตราการชำรุดเสียหาย(Failure rate) 0.1 % นั่นคือ แต่ละวันเครื่องจักรทั้งระบบ 100 เครื่องเกิดการชำรุดขัดข้องรวม 1000 ครั้ง หากใช้เวลา 30 วินาทีสำหรับแก้ปัญหาการขัดข้องที่เกิดขึ้นแต่ละครั้งอาจต้องใช้เวลากว่า 8 ชั่วโมงเพื่อแก้ปัญหาเครื่องจักรทั้งหมด ดังนั้นโรงงานบางแห่งจึงได้กำหนดว่าหากไม่สามารถแก้ปัญหาเหล่านี้ภายในช่วงเวลาที่กำหนดก็ถือว่าเป็นปัญหาการ Breakdown เช่น ความผิดปกติที่เกิดกับเครื่องจักรช่วงระหว่างเดินเครื่อง ทำให้ต้องปรับตั้งความเยื้องศูนย์(Mis-Alignment) หรือการใช้ V-MER Smart Vibration Analyzer ตรวจวัดความสั่นสะเทือน(Vibration) ด้วยสภาพปัญหาดังกล่าวอาจจัดว่าเป็นความผิดพลาดจากกระบวนการซึ่งนับเป็นจำนวนครั้งการหยุดเดินเครื่องจักรเล็กน้อย นี่คือ ประเด็นหนึ่งที่ต้องพิจารณากำหนดแนวทางปรับปรุงต่อไป
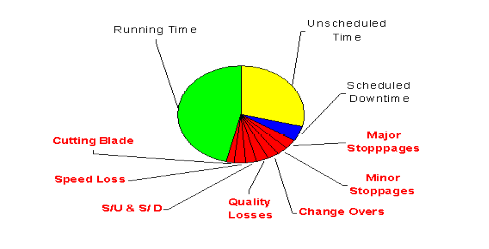
การจำแนกประเภทความสูญเสีย
ช่วงหลายทศวรรษที่ผ่านมาได้มีการใช้ค่า MTBF(Mean Time Between Failure) แสดงค่าเฉลี่ยระยะเวลาปฏิบัติงาน(Operating time) เพื่อปรับปรุงสายการผลิตแบบอัตโนมัติ นับแต่นั้นมาก็ได้มีการใช้ค่า MTBF ชี้วัดอัตราการหยุดเดินเครื่องจักร ซึ่ง MTBF เป็นอัตราส่วนที่ผกผันกับอัตราการเกิด Breakdown ดังนั้นอัตราการเกิด Breakdown เป็นปัจจัยหนึ่งของการประเมินความน่าเชื่อถือระบบ(Process Reliability) โดยช่วงเวลาปฏิบัติงาน(OT) แสดงด้วย วัน สัปดาห์ และเดือน ส่วน Nf แทนด้วยจำนวนครั้งการเกิดปัญหา Breakdown ระหว่างช่วงการเดินเครื่องจักร ดังนั้นค่า MTBF แสดงด้วยความสัมพันธ์ ดังนี้
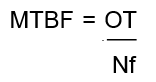
หาก MTBF มีสัดส่วนสูงนั่นเป็นการบ่งชี้ถึงสภาพเครื่องจักรมีความน่าเชื่อถือสูง ด้วยเหตุนี้ MTBF ถูกใช้เป็นตัวชี้วัดความน่าเชื่อถือ โดยเฉพาะการรับประกันการใช้งานตามข้อกำหนดที่ระบุไว้ ดังนั้นความถี่หรือจำนวนครั้งการชำรุดขัดข้องถูกแทนด้วยจำนวนครั้งของ Minor Stoppage ภายในช่วงรอบเวลาเดินเครื่องจักร ซึ่งคำนวณได้จากความสัมพันธ์ ดังนี้

สำหรับช่วงระยะเวลาจัดเก็บข้อมูลเพื่อประเมิน MTBF ควรมากกว่าหนึ่งสัปดาห์ขึ้นไปเพื่อให้ผลลัพธ์การประเมินมีความแม่นยำ โดยทั่วไปมักใช้รอบเวลาประมาณหนึ่งเดือน ซึ่งข้อมูลที่จัดเก็บประกอบด้วย
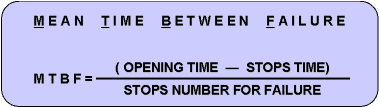
- รอบเวลาการเดินเครื่อง โดยจัดเก็บบันทึกข้อมูลด้วยเครื่องตรวจนับ(Counter) สำหรับเครื่องตรวจนับจำแนกได้ คือ เครื่องนับค่าเวลาปฏิบัติงานซึ่งเหมาะสำหรับบันทึกเพื่อประเมินค่า MTBF และเครื่องนับเวลาการหยุดเดินเครื่อง(Downtime) หากรอบเวลา(Cycle Time) ไม่มีความผันผวนสามารถวัดรอบเวลาเพื่อคำนวณเวลาการเดินเครื่องจักร ดังนี้
เวลาการเดินเครื่อง = รอบเวลาจริง x จำนวนชั่วโมงการทำงาน(Nk)
- จำนวนครั้งการขัดข้องเล็กน้อย เนื่องจากผู้ปฏิบัติงานจะมุ่งแก้ปัญหาเมื่อเกิดปัญหาจากการหยุดเดินเครื่องจักรจึงไม่สามารถจดบันทึกข้อมูลได้อย่างครบถ้วน ดังนั้นจึงนิยมใช้ Counter แทนการบันทึกด้วยมือ(Manual Record) หากเครื่องนับค่าสามารถวัดได้เพียงจำนวนครั้งการหยุดเดินสายการผลิต(Shutdown) แต่ไม่สามารถจำแนกสาเหตุความคลาดเคลื่อนว่าเป็นการหยุดเดินเครื่องเล็กน้อยหรือเกิดจากสาเหตุอื่นๆ สามารถใช้สูตรคำนวณจำนวนครั้งการหยุดเดินเครื่องเล็กน้อย ดังนี้
Nf = ผลรวมการหยุดสายการผลิต – การหยุดสายการผลิตที่เกิดจากสาเหตุอื่นๆ
สำหรับการหยุดสายการผลิตที่เกิดจากสาเหตุอื่น ๆ ที่ไม่เกี่ยวกับความผิดปกติ ได้แก่ เวลาเสร็จสิ้นการทำงานแต่ละกะทำงาน การหยุดเดินเครื่องจักรเนื่องจากการหยุดพัก การหยุดเดินเครื่องจักรช่วงการเปลี่ยนรุ่นการผลิต(Changeover) การหยุดเพื่อถอดเปลี่ยนชิ้นส่วนตามรอบเวลา(Replacement) แต่หากการหยุดสายการผลิตเนื่องจากการแตกหักของเครื่องมือหรือตัวจับยึดจัดว่าเป็น Minor Stoppages ส่วนค่าเฉลี่ย MTBF เกิดจากการวัดค่า MTBF แต่ละกระบวนการ นั่นคือ บางกระบวนการมีค่า MTBF สูงกว่าหรือต่ำกว่าค่าเฉลี่ย โดยค่าเฉลี่ย MTBF หาได้จาก

- ประสิทธิผลอัตราการใช้กำลังการผลิต(Effective Capacity Utilization) เนื่องจากการเพิ่มอัตราการเดินเครื่องเป็นผลจากการลดปัญหา Minor Stoppage ตามที่ Dr.Masakatsu Nakaigawa นิยามความสัมพันธ์ประสิทธิผลอัตราการใช้กำลังการผลิต ดังนี้

โดยทั่วไปความสูญเสียหลักจากปัญหา Minor Stoppage ได้แก่ ต้นทุนการผลิตสูงขึ้น การเกิดของเสียจากกระบวนการผลิตและปัญหาส่งมอบสินค้าให้กับลูกค้าล่าช้า รวมถึงอาจเกิดผลกระทบด้านความปลอดภัยซึ่งส่งผลต่อขวัญและกำลังใจของผู้ปฏิบัติงาน ดังนั้นจึงต้องหาแนวทางลดความถี่การเกิดปัญหา Minor Stoppage โดยดำเนินการตามขั้นตอน ดังนี้
- กำหนดเป้าหมายและหัวข้อปัญหาหลัก โดยมุ่งลดความถี่การเกิดปัญหา Minor Stoppage ด้วยการจัดทำเอกสารข้อเสนอ(Proposal) เพื่ออธิบายสภาพปัญหาที่เกิดขึ้นและเสนอประเด็นการปรับปรุง ตลอดจนกำหนดมาตรวัดติดตามผลการดำเนินโครงการ ดังนั้นเป้าหมายโครงการปรับปรุงควรครอบคลุมถึง การลดจำนวนแรงงานในสายการผลิตอัตโนมัติ การเพิ่มผลิตภาพกระบวนการและการเชื่อมโยงระหว่างเครื่องจักรในสายการผลิต รวมถึงการจัดตั้งทีมงานปรับปรุงประกอบด้วยผู้ควบคุมเครื่องจักรและผู้ชำนาญการจากฝ่ายงานเกี่ยวข้อง เช่น วิศวกร ช่างเทคนิค เจ้าหน้าที่งานบำรุงรักษา และผู้จัดการฝ่ายคุณภาพ
- ประเมินค่า MTBF ด้วยการรวบรวมข้อมูลการหยุดเดินเครื่องจักรและดำเนินการติดตามวัดผลต่อเนื่องกระทั่งบรรลุผลตามเป้าหมาย โดยข้อมูลสำคัญจากการประเมินวัดผลควรประกอบด้วย สถิติค่า MTBF ที่จัดเก็บตามรอบเวลาและวิเคราะห์สาเหตุหลักการเกิดปัญหาหยุดเดินเครื่องจักรเพื่อแสดงให้ผู้ปฏิบัติงานทราบความก้าวหน้าโครงการปรับปรุง ทำให้สามารถวิเคราะห์แนวโน้มปัญหาที่เกิดขึ้น
- กำหนดค่าเป้าหมายเพื่อเทียบเคียง(Benchmark) โดยเทียบค่า MTBF ระหว่างก่อนและหลังการปรับปรุง โดยทั่วไปกำหนดเป้าหมายด้วยการลดของเสียที่ระดับ 1/10 และลดความถี่การเกิดปัญหา Minor Stoppage ที่ระดับ 1/20 เทียบกับช่วงก่อนปรับปรุง(เพิ่มสัดส่วนค่า MTBF สูงขึ้น 20 เท่า)
- ติดตามตรวจสอบเป้าหมายกระบวนการ ช่วงนี้มีความสำคัญสำหรับการเริ่มดำเนินการลดปัญหาหยุดเดินเครื่องจักรด้วยการศึกษาหลักการทางวิศวกรรมเพื่อจำแนกสาเหตุการเกิดปัญหาอย่างชัดเจนและสามารถดำเนินโครงการปรับปรุงอย่างมีประสิทธิผล โดยทีมงานควรศึกษารูปแบบปัญหาจากแหล่งข้อมูล ดังนี้
- คู่มือการใช้งาน เพื่อเข้าใจถึงโครงสร้าง และกลไกการทำงานของเครื่องจักร
- รายละเอียดข้อกำหนดและมาตรฐานที่เกี่ยวข้องตลอดจนข้อเสนอแนะจากวิศวกร
- การสนทนาแลกเปลี่ยนประสบการณ์ระหว่างผู้เชี่ยวชาญกับทีมงาน
- การตรวจสอบสภาพเครื่องจักรด้วยกิจกรรมทำความสะอาด ทำให้สามารถมองเห็นจุดบกพร่องที่ผู้ปฏิบัติงานมักมองข้าม อาทิ
– การขันยึดแน่นอุปกรณ์ที่มีผลกับความปลอดภัย เช่น น็อต สกรู โดยทำเครื่องหมายแสดงจุดที่เกิดปัญหา เพื่อสังเกตได้ง่ายเมื่อทำการขันยึดอีกครั้ง
– การหล่อลื่นจัดเป็นส่วนสำคัญของกิจกรรมบำรุงรักษา โดยเฉพาะบริเวณรางลื่นและพื้นที่ผิวสัมผัสของการหมุน
– การชำรุดเสียหายของอุปกรณ์เกจวัด
5. ทีมงานดำเนินการวิเคราะห์ผลเพื่อจำแนกสาเหตุหลักและกำหนดประเด็นหัวข้อสำหรับปรับปรุงหลังจากได้ติดตามบันทึกปัญหาที่เกิดขึ้น
6. นำข้อมูลขั้นตอนที่ 4 และผลการวิเคราะห์ขั้นที่ 5 เพื่อกำหนดสาเหตุปัญหาหลัก(Specific Cause)ของการเกิด Minor Stoppage ด้วยการวิเคราะห์ความสัมพันธ์ระหว่างเหตุและผล เพื่อใช้ร่างแผนปฎิบัติการบำรุงรักษาและดำเนินการปรับปรุงอย่างเป็นรูปธรรม
7. ดำเนินกิจกรรมปรับปรุงตามวงจร PDCA อย่างต่อเนื่องจนบรรลุเป้าหมายตามประเด็นหัวข้อที่กำหนด
8. ดำเนินการติดตามผลอย่างต่อเนื่องเพื่อดำเนินการจัดทำเป็นมาตรฐาน(Standardize) โดยมุ่งให้พนักงานระดับปฏิบัติการเข้าใจบทบาทความมีส่วนร่วมในกิจกรรมดังกล่าวด้วยการนำเสนอบทเรียนจากปัญหา หรือ One Point Lesson ทำให้สามารถเรียนรู้แนวทางแก้ไขได้อย่างรวดเร็วและป้องกันไม่ให้ปัญหาเดิมเกิดขึ้นอีก
สำหรับท่านที่สนใจเนื้อหาสาระและข้อมูลดี ๆ ด้านการบำรุงรักษาหรือโซลูชั่นส์และงานบริการต่าง ๆ สามารถลงทะเบียนได้ฟรีและติดตามข้อมูลข่าวสารทางเว็บไซต์ www.esspower.com