โกศล ดีศีลธรรม
ผู้จัดการทั่วไป(General Manager)
บริษัท อีควิตี้ เซอร์วิสเซส แอนด์ โซลูชั่นส์ จำกัด(Equity Services and Solutions)
ปัญหาความผันผวนผลิตผลมักเกิดจากปัญหาเครื่องจักรขัดข้อง(Breakdown) หากเกิดปัญหาเครื่องจักรขัดข้องก็จะส่งผลกระทบต่อกระบวนการถัดไปและอาจรุนแรงถึงต้องหยุดเดินสายการผลิต ดังนั้นการใช้เวลาแก้ไขปัญหานานจะทำให้เกิดงานระหว่างผลิตในรูปสต็อกค้าง ทำให้ส่งผลต่อความน่าเชื่อถือและความปลอดภัยในสายการผลิต ทำให้งานบำรุงรักษาเป็นปัจจัยสนับสนุนความน่าเชื่อถือกระบวนการ โดยเฉพาะการบำรุงรักษาเชิงรุกที่มีบทบาทสำคัญในการป้องกันปัญหาเครื่องจักรขัดข้องและเป็นปัจจัยสนับสนุนการสร้างความน่าเชื่อถือให้กระบวนการ ทำให้เกิดการพัฒนาผลิตภาพ ดังนี้
- เกิดความสะอาดและความปลอดภัยในสถานที่ทำงาน
- การจำแนกปัญหาซ้อนเร้นในสายการผลิตและสามารถดำเนินการแก้ไขโดยทีมงานบำรุงรักษา
- การพัฒนาทักษะความรู้ที่เกิดจากการทำงานร่วมกันอย่างใกล้ชิดระหว่างช่างเทคนิคกับผู้ชำนาญการและวิศวกร ทำให้เกิดการเรียนรู้และถ่ายทอดทักษะระหว่างกัน
- เกิดการพัฒนาวิธีการทำงานอย่างมีประสิทธิภาพ
- ประสิทธิผลการเดินเครื่องจักรทำให้เกิดการพัฒนาความสามารถการแข่งขัน
- การพัฒนาคุณภาพผลิตภัณฑ์ทำให้เกิดของเสียและงานแก้ไขน้อยลง ผลลัพธ์ดังกล่าวไม่เพียงแค่ส่งผลต่อการลดต้นทุนการผลิตเท่านั้น แต่ยังสร้างความพึงพอใจให้กับลูกค้า
ด้วยเหตุนี้กิจกรรมบำรุงรักษา คือ ส่วนหนึ่งกระบวนการสร้างความน่าเชื่อถือให้เครื่องจักรพร้อมใช้งานด้วยการดำเนินกิจกรรมบำรุงรักษาก่อนจะเกิดเหตุขัดข้อง อาทิ การบำรุงรักษาประจำวัน การปรับแต่งเครื่อง การตรวจเช็คและถอดเปลี่ยนอะไหล่ตามรอบเวลา การปรับปรุงวิธีการปฏิบัติงานที่มุ่งความปลอดภัยและการป้องกันไม่ให้ปัญหาเดิมเกิดขึ้นอีก ซึ่งการประเมินประสิทธิผลการบำรุงรักษาจะใช้ตัวชี้วัดความสูญเสียกำลังการผลิตและการหยุดเดินเครื่องจักรที่ไม่มีในแผน(Unplanned Shutdown) ดังนั้นประสิทธิผลงานบำรุงรักษาจะเกิดขึ้นก็ต่อเมื่อสามารถลดความสูญเสียจากเครื่องจักรขัดข้อง แต่จะมีแนวทางใดบ้างที่ยืนยันว่าการดำเนินกิจกรรมบำรุงรักษาเกิดประสิทธิผลในช่วงเวลาที่เหมาะสม ดังนั้นการประเมินประสิทธิผลควรประกอบด้วย
- การกำหนดเป้าหมาย เนื่องจากการบำรุงรักษาเชิงแก้ไขถือเป็นองค์ประกอบหนึ่งในโครงการบำรุงรักษาเชิงป้องกันที่มุ่งการแก้ไขความขัดข้องในองค์ประกอบเครื่องจักรที่ถูกใช้เป็นตัวชี้วัดประสิทธิผลงานบำรุงรักษาเชิงป้องกัน การกำหนดเป้าหมายกิจกรรมบำรุงรักษาเชิงแก้ไขควรระบุตามสัดส่วนการบำรุงรักษาเชิงป้องกัน ซึ่งปริมาณหรือสัดส่วนที่เหมาะสมขึ้นกับข้อกำหนดมาตรฐานเครื่องจักร โดยต้องมีจัดเก็บข้อมูลเพื่อใช้ประเมินผลและทบทวนแนวโน้มการสึกหรอแต่ละองค์ประกอบของเครื่องจักร
- ประเมินประสิทธิผล โดยใช้ข้อมูลที่จัดเก็บเพื่อประเมินความถี่ปัญหาเดิมที่มักเกิดขึ้นซ้ำอีกซึ่งจะถูกนำมาวิเคราะห์หาสาเหตุหลักเพื่อดำเนินการขจัดออก บางกรณีอาจใช้แนวทางบำรุงรักษาเชิงคาดการณ์เพื่อติดตามข้อมูลสภาพเครื่องจักรและประเมินแนวโน้มความชำรุด อาทิ การใช้อุปกรณ์ V-MER Smart Vibration Analyzer วิเคราะห์ความสั่นสะเทือนเครื่องจักร ข้อมูลเหล่านี้จะถูกใช้บ่งชี้องค์ประกอบหรือชิ้นส่วนที่ต้องปรับปรุงหรือการถอดเปลี่ยนก่อนที่จะเกิดความชำรุดเสียหาย
- วิเคราะห์ความเสียง โดยนำข้อมูลองค์ประกอบรวมของเครื่องจักรที่ถูกจัดเก็บในฐานข้อมูลสินทรัพย์โรงงานเพื่อใช้ประเมินความเสี่ยงที่มีผลต่อโรงงาน โดยมีการติดตามประเมินผลรายเดือน ผลการประเมินจะถูกใช้ทบทวนกิจกรรมบำรุงรักษา โดยมีการระบุองค์ประกอบหลักที่มีผลกระทบต่อระบบความน่าเชื่อถือระดับโรงงานและลำดับความสำคัญแต่ละองค์ประกอบไว้ในแผนงานบำรุงรักษา
- วิเคราะห์ค่าใช้จ่ายเทียบกับผลตอบแทนด้วยการติดตามจัดเก็บข้อมูลเกี่ยวกับชั่วโมงทำงาน ที่ถูกใช้ในกิจกรรมแก้ไขและค่าใช้จ่ายต่าง ๆ อาทิ ค่าโสหุ้ย ค่าอะไหล่ ซึ่งมีการแสดงผลรายเดือน รวมทั้งประมาณค่าใช้จ่ายรายปี ข้อมูลเหล่านี้จะถูกใช้วิเคราะห์ค่าใช้จ่ายเทียบกับผลตอบแทนเพื่อนำมาใช้พัฒนากลยุทธ์การบำรุงรักษา
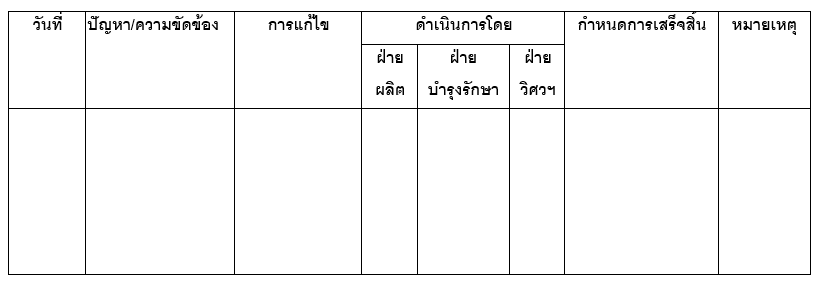
ตัวอย่างแบบฟอร์มบันทึกปัญหา
สำหรับเครื่องจักรที่มีความซับซ้อนและเกิดปัญหาขัดข้องหรือหยุดเดินเครื่องขณะกำลังเดินสายการผลิตจะส่งผลกับค่าแรงงานบำรุงรักษาและค่าอะไหล่ถอดเปลี่ยน ดังนั้นการออกแบบเครื่องจักรควรพิจารณาปัจจัยความสะดวกในการให้บริการซ่อมบำรุงและประสิทธิผลต้นทุนในการฟื้นฟูสภาพเครื่องจักรให้ใช้งานได้ตามปกติ รวมทั้งเกิดความน่าเชื่อถือของระบบ(Reliability)และความมีส่วนร่วมของฝ่ายงานบำรุงรักษา หากระบบมีความน่าเชื่อถือก็จะส่งผลให้เกิดปัญหาความขัดข้องลดลง ดังนั้นประสิทธิผลการออกแบบจะมุ่งให้เกิดความสะดวกต่อการถอดเปลี่ยนด้วยการแยกระบบออกเป็นองค์ประกอบตามหน้าที่การใช้งาน(Modular Design)และการดัดแปลงองค์ประกอบเครื่องจักรให้สะดวกในการเข้าถึงจุดปฏิบัติงานบำรุงรักษาเพื่อลดเวลาและต้นทุนดำเนินงาน ทำให้เกิดแนวคิดการออกแบบป้องกันการบำรุงรักษา(Maintenance Prevention) ที่มุ่งลดปัญหาเครื่องจักรหลังการติดตั้งให้น้อยที่สุดซึงถือเป็นปัจจัยหนึ่งของตันทุนวงจรอายุ ส่วนการประเมินเชิงเศรษฐศาสตร์ระหว่างช่วงการออกแบบมีความจำเป็นที่ต้องใช้ฐานข้อมูลแสดงรายการต้นทุนการเดินเครื่อง โดยให้ความสำคัญกับการจัดเก็บข้อมูลดิบเพื่อใช้คำนวณต้นทุน ข้อมูลที่ถูกใช้พิจารณา ได้แก่
- ข้อมูลความน่าเชื่อถือของระบบหรือชิ้นส่วนหลัก อาทิ MTBF(Mean Time Between Failure)
- ข้อมูลเกี่ยวกับการขัดข้อง เช่น เวลาหยุดเดินเครื่องจักร ชั่วโมงแรงงานที่ใช้ในงานซ่อมบำรุง(Man-Hour) และค่าใช้จ่ายการบำรุงรักษาเชิงป้องกัน
- แนวโน้มอัตราการเกิดของเสีย(Defect Rate)
- เวลาที่ถูกใช้สำหรับการเปลี่ยนรุ่นการผลิต(Changeover Time)
- ปัจจัยผลิตภาพการปฏิบัติงาน อาทิ ปริมาณวัสดุที่ถูกใช้ต่อหน่วยผลิตผล ค่าพลังงานต่อหน่วย
นอกจากนี้ควรพิจารณาการนำเทคโนโลยีเพื่อใช้ตรวจติดตามระบบการผลิตและเก็บข้อมูลสภาพเครื่องจักรขณะใช้งานโดยมุ่งวิเคราะห์แนวทางป้องกัน โดยบูรณาการเทคนิคการจัดการและเทคโนโลยีเพื่อวิเคราะห์และระบุหาแนวทางแก้ไขปัญหาที่มีประสิทธิผล รวมถึงเชื่อมโยงกับระบบวางแผนบำรุงรักษา ทำให้ระบบการผลิตและเครื่องจักรเกิดความน่าเชื่อถือซึ่งส่งผลให้เกิดต้นทุนการผลิตลดลง แต่สิ่งสำคัญในการบริหารงานบำรุงรักษา คือ การสร้างสมดุลระหว่างค่าใช้จ่ายงานบำรุงรักษากับผลตอบแทนเพื่อไม่ให้เกิดการลงทุนที่เกินความจำเป็น ส่วนระบบการวัดผลจะบ่งบอกสภาพเครื่องจักรและต้องมีการตรวจติดตามสภาพต่อเนื่องเพื่อรับข้อมูลความเปลี่ยนแปลงและใช้เทียบเคียงตามรอบเวลาเพื่อแสดงแนวโน้มระบบในรูปแบบรายงานผล โดยเฉพาะข้อมูลความเสื่อมสภาพจะถูกนำมาวิเคราะห์หาสาเหตุหลักความขัดข้อง(Root Cause Analysis) ทำให้วิศวกรบำรุงรักษาเข้าใจสภาพปัญหาและนำข้อมูลเหล่านี้มาใช้วางแผนบำรุงรักษาเพื่อป้องกันไม่ให้เกิดปัญหาเดิมอีก ทั้งยังใช้เป็นเครื่องมือลดค่าใช้จ่ายที่ไม่จำเป็น
สำหรับท่านที่สนใจเนื้อหาสาระและข้อมูลดี ๆ ด้านการบำรุงรักษาหรือโซลูชั่นส์และงานบริการต่าง ๆ สามารถลงทะเบียนและติดตามที่เว็บไซต์ www.esspower.com