โกศล ดีศีลธรรม
ผู้จัดการทั่วไป(General Manager)
บริษัท อีควิตี้ เซอร์วิสเซส แอนด์ โซลูชั่นส์ จำกัด(Equity Services and Solutions)
เนื่องจากปัญหาเครื่องจักรขัดข้องจะส่งผลกระทบโดยตรงกับสายการผลิต โดยเฉพาะธุรกิจภาคอุตสาหกรรม ปัจจัยสนับสนุนการสร้างความน่าเชื่อถือให้ระบบการผลิต คือ การดำเนินกิจกรรมบำรุงรักษาที่มุ่งป้องกันการเกิดปัญหาเครื่องจักรขัดข้องและการซ่อมแซมอย่างทันท่วงทีเพื่อลดความสูญเสียขณะใช้งาน ดังนั้นความรับผิดชอบของวิศวกรบำรุงรักษาต้องมุ่งค้นหาจำแนกสาเหตุหลักปัญหาเพื่อระบุแนวทางแก้ปัญหาด้วยเทคนิควิศวกรรมความน่าเชื่อถือ(Maintenance Engineering) ประกอบด้วยแนวทางและเครื่องมือหลัก ดังนี้
- การวิเคราะห์หาสาเหตุหลักการชำรุดเสียหาย(Root Cause Failure Analysis) หรือ RCFA เป็นหน้าที่หลักของวิศวกรบำรุงรักษา โดยการวิเคราะห์สาเหตุหลักและประเภทปัญหาความบกพร่องในกระบวนการซึ่งส่งผลกระทบต่อเวลาการเดินเครื่องจักรและคุณภาพผลิตผลได้มีการปรับเปลี่ยนแนวคิดจากการควบคุมคุณภาพสู่การประกันคุณภาพด้วยการศึกษาองค์ประกอบหลักเครื่องจักรที่ส่งผลต่อคุณภาพผลิตผลและขจัดต้นตอปัญหาดังกล่าว ซึ่งมีการติดตามวัดผลตามรอบเวลาเพื่อใช้ข้อมูลดำเนินกิจกรรมไคเซ็นและจัดเก็บข้อมูลที่จำเป็น โดยมีรายละเอียดข้อมูลเกี่ยวกับผลิตภัณฑ์ อาทิ ตำแหน่งที่เกิดปัญหาความบกพร่อง ความรุนแรงแต่ละประเภทปัญหา ความถี่การตรวจพบปัญหาแต่ละช่วงการทดสอบและแนวโน้มการเกิดปัญหาคุณภาพตามรอบเวลา ส่วนข้อมูลเกี่ยวกับกระบวนการ โดยเฉพาะเงื่อนไขการทำงานแต่ละกระบวนการ เช่น แรงงาน วิธีการทำงาน วัสดุ และเครื่องจักร การกำหนดมาตรฐานหรือเงื่อนไขการทำงานแต่ละกระบวนการ ข้อมูลที่บันทึกเกี่ยวกับสภาพการทำงานขณะที่เกิดปัญหาขึ้น โดยองค์ประกอบหรือชิ้นส่วนหลักถูกระบุไว้ในระบบย่อย(Sub-system) โดยใช้ข้อมูลประวัติการขัดข้องและการซ่อมแซมจากความชำรุดดังกล่าวที่อาจเป็นสาเหตุความชำรุดในระบบย่อย โดยเฉพาะกรณีรูปแบบความชำรุดเสียหายซ่อนเร้นที่ส่งผลต่อกระทบต่อความปลอดภัยในการทำงาน ส่วนค่าใช้จ่ายทั้งทางตรงและทางอ้อมในงานบำรุงรักษาควรน้อยกว่าค่าความชำรุดเสียหายทั้งทางตรงและทางอ้อมของผลกระทบที่เกิดจากความชำรุดเสียหายรวมกับค่าซ่อมแซม เมื่อทำการวัดเปรียบเทียบตลอดอายุการใช้งาน(Life Cycle)
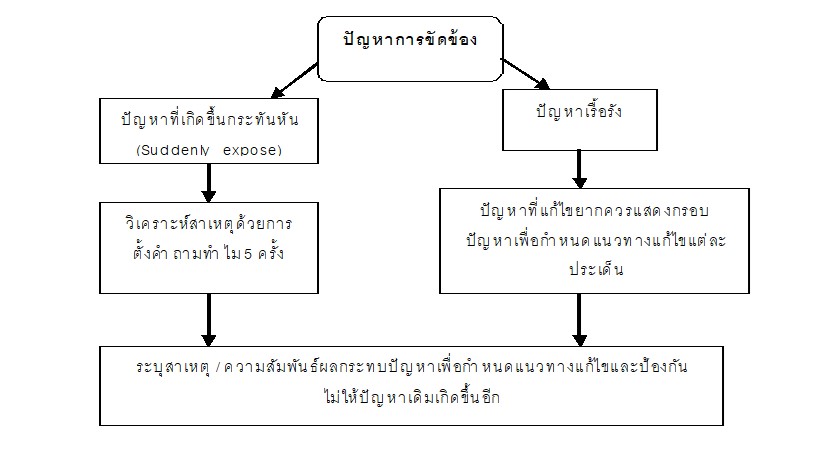
กระบวนการวิเคราะห์ปัญหาเครื่องจักร
- การวิเคราะห์ความชำรุดของชิ้นส่วน(Fail Part Analysis) โดยทดสอบความน่าเชื่อถือองค์ประกอบหรือชิ้นส่วนหลักที่ส่งผลกระทบต่อระบบและดำเนินการถอดเปลี่ยนก่อนที่จะเกิดความชำรุดเสียหายซึ่งมักดำเนินการทดสอบทางกายภาพหรือปัจจัยสภาพแวดล้อมที่ส่งผลต่อการเสื่อมสภาพ เช่น การกัดกร่อน(Corrosion) ทั้งยังวิเคราะห์ผลกระทบความชำรุดเสียหายด้วย FMEA เพื่อกำหนดแนวทางป้องกัน รวมถึงการทดสอบความน่าเชื่อถือชิ้นส่วนหลัก(Critical Component) ที่ส่งผลกระทบต่อระบบโดยรวมเพื่อทำการถอดเปลี่ยนก่อนที่จะเกิดความชำรุดเสียหายขึ้น ส่วนขั้นตอนวิเคราะห์เริ่มจากการระบุรายละเอียดการใช้งานและองค์ประกอบส่วนต่าง ๆ โดยรูปแบบความชำรุดเสียหาย(Failure Mode) อาทิ ความล้า การรั่ว การโก่ง จะถูกจำแนกและลำดับตามความรุนแรงที่ประเมินจากค่า Risk Priority Number(RPN) ข้อมูลเหล่านี้จะถูกใช้จัดทำคู่มือเพื่อสนับสนุนการทำงาน อาทิ มาตรฐานการทำงาน คู่มือออกแบบ รายการตรวจสอบ(Checklist) สำหรับองค์ประกอบหรือชิ้นส่วนหลักถูกระบุไว้ในระบบย่อยโดยใช้ข้อมูลประวัติการขัดข้องและการซ่อมแซมจากความชำรุดดังกล่าวที่อาจเป็นสาเหตุความชำรุดในระบบย่อย โดยรูปแบบความชำรุดเสียหายแต่ละองค์ประกอบถูกระบุเพื่อประเมินวัดความเสี่ยงโดยลำดับตามค่าวิกฤตความชำรุดเสียหายในการใช้งาน(Functional Failure)
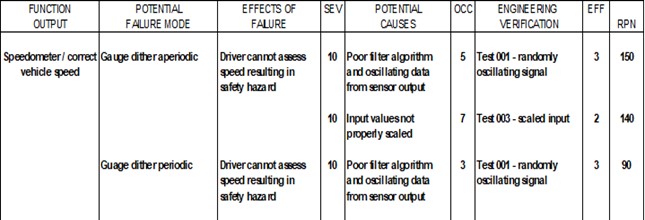
การวิเคราะห์รูปแบบความชำรุดเสียหาย(FMEA)
- การวิเคราะห์ประสิทธิผลวิธีการบำรุงรักษา(Maintenance Procedure Effectiveness Analysis) โดยใช้ข้อมูลรายงานจากระบบ CMMS เช่น ความถี่การเกิดปัญหา มาตรฐานวิธีการแก้ปัญหา ชิ้นส่วนหลักที่เกิดปัญหาบ่อย เป็นต้น ซึ่งนำข้อมูลเหล่านี้มาวิเคราะห์ประเมินแนวโน้มปัญหาเพื่อดำเนินการปรับปรุงมาตรฐานวิธีการบำรุงรักษาอย่างเหมาะสม เช่น การระบุรอบความถี่งานบำรุงรักษาเชิงป้องกันและประเมินรอบเวลาการยกเครื่องใหญ่(Overhaul Maintenance) โดยจัดทำเป็นเอกสารเพื่อใช้เป็นแนวทางปฏิบัติงานซึ่งมีการทบทวนต่อเนื่องเพื่อมุ่งการยืดอายุการใช้งาน
- วิเคราะห์แนวโน้มการตรวจติดตามสภาพ(Trending and Analysis of Condition Monitoring) เป็นองค์ประกอบหนึ่งของการบำรุงรักษาเชิงคาดการณ์(Predictive Maintenance) โดยนำผลลัพธ์การตรวจติดตามสภาพเครื่องจักรมาวิเคราะห์เพื่อระบุข้อกำหนดทางปัจจัยเดินเครื่อง อาทิ อุณหภูมิ ความเร็วรอบ และรอบเวลาบำรุงรักษาที่เหมาะสม โดยมีการนำเทคโนโลยีที่ใช้ติดตามระบบการผลิตและจัดเก็บข้อมูลสภาพเครื่องจักรขณะใช้งานโดยมุ่งวิเคราะห์แนวทางป้องกันก่อนที่จะเกิดเหตุขัดข้องหรือความเสียหายด้วยการบูรณาการเทคนิคการจัดการและเทคโนโลยีเพื่อวิเคราะห์และระบุหาแนวทางแก้ไขปัญหาที่มีประสิทธิผล รวมถึงเชื่อมโยงกับระบบวางแผนบำรุงรักษา ทำให้ระบบการผลิตเกิดความน่าเชื่อถือและส่งผลให้เกิดต้นทุนการผลิตลดลง ดังกรณีการใช้อุปกรณ์ V-MER Smart Vibration Analyzer วิเคราะห์ความสั่นสะเทือนเครื่องจักร ข้อมูลเหล่านี้จะถูกใช้บ่งชี้องค์ประกอบหรือชิ้นส่วนที่ต้องปรับปรุงหรือการถอดเปลี่ยนในเวลาที่เหมาะสม
แต่สิ่งสำคัญในการบริหารงานบำรุงรักษา คือ การสร้างสมดุลระหว่างค่าใช้จ่ายบำรุงรักษากับผลตอบแทนเพื่อไม่ให้เกิดการลงทุนที่เกินความจำเป็น ดังนั้นการเพิ่มสมรรถนะเครื่องจักรและลดค่าใช้จ่ายบำรุงรักษาเป็นประเด็นหลักของระบบสารสนเทศ ซึ่งประสิทธิผลจะเกิดขึ้นก็ต่อเมื่อระบบสารสนเทศงานบำรุงรักษาสามารถยืดช่วงเวลาเฉลี่ยการเกิดความเสียหาย(Mean Time Between Failure)และสามารถลดเวลาเฉลี่ยการซ่อมแซม(Mean Time To Repair) โดยทั้ง MTBF และ MTTR เป็นปัจจัยสร้างความน่าเชื่อถือและความพร้อมระบบ(Availability) ส่วนองค์ประกอบหลักที่จำเป็นต่อระบบสารสนเทศงานบำรุงรักษา คือ สารสนเทศงานออกแบบ กฏระเบียบด้านความปลอดภัย การควบคุมการปฏิบัติการ การวางแผนวิเคราะห์ความน่าเชื่อถือ การติดตามประเมินสภาพเครื่องจักร การจัดหาจัดซื้อและบริหารสต็อก ส่วนระบบการวัดผลจะบ่งบอกสภาพเครื่องจักร ดังนั้นการวัดผลจะต้องมีการตรวจติดตามสภาพต่อเนื่องเพื่อรับข้อมูลความเปลี่ยนแปลงและใช้เทียบเคียงตามรอบเวลาเพื่อแสดงแนวโน้มระบบในรูปรายงานผล โดยเฉพาะข้อมูลความเสื่อมสภาพจะถูกนำมาวิเคราะห์หาสาเหตุหลักความขัดข้อง ทำให้วิศวกรบำรุงรักษาเข้าใจสภาพปัญหาและนำข้อมูลเหล่านี้มาใช้วางแผนบำรุงรักษาเพื่อป้องกันไม่ให้เกิดปัญหาเหล่านี้เกิดขึ้นอีก ทั้งยังใช้เป็นเครื่องมือลดค่าใช้จ่ายที่ไม่จำเป็น
อุปกรณ์ V-MER Smart Vibration Analyzer
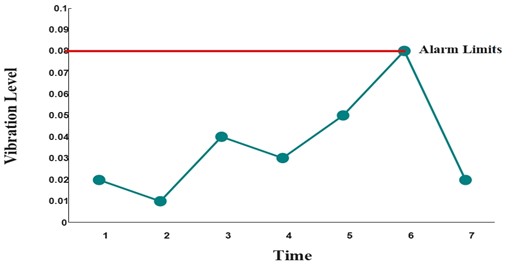
แสดงแนวโน้มการติดตามสภาพเครื่องจักร
สำหรับท่านที่สนใจเนื้อหาสาระและข้อมูลดี ๆ ด้านการบำรุงรักษาหรือโซลูชั่นส์และงานบริการต่าง ๆ ของ บริษัท อีควิตี้ เซอร์วิสเซส แอนด์ โซลูชั่นส์ จำกัด สามารถลงทะเบียนและติดตามที่เว็บไซต์ www.esspower.com